In the intricate world of electrical engineering, every component plays a crucial role in ensuring the seamless operation of machines and devices. One such indispensable element is the rotor winding copper strip, a key player in the heart of electric motors and generators. In this blog post, we'll delve into the fascinating realm of rotor winding copper strips, exploring their significance, manufacturing process, and the vital role they play in the functioning of various electrical systems.
The Significance of Rotor Winding Copper Strips:
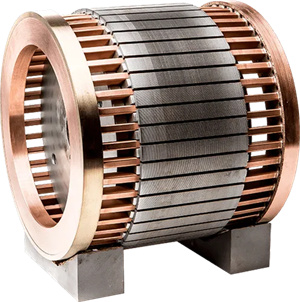
Rotor winding copper strips serve as the lifeline of electric motors and generators, facilitating the flow of electrical currents within these devices. These strips are an integral part of the rotor, which is the rotating component in the heart of these machines. The importance of copper in this context lies in its excellent conductivity, durability, and malleability, making it an ideal material for transmitting electrical energy efficiently.
Manufacturing Process:
The production of rotor winding copper strips is a meticulous process that demands precision and expertise. Here's an overview of the key steps involved in manufacturing these crucial components:
Copper Selection:
High-quality copper is the foundation of efficient rotor winding. Manufacturers often opt for oxygen-free copper due to its superior conductivity and reduced risk of oxidation.
Stripping and Shaping:
The copper is then stripped into thin strips and shaped according to the specific design requirements of the rotor. This step involves cutting, rolling, and sometimes heat treatment to achieve the desired dimensions.
Insulation Coating:
To prevent short circuits and ensure the longevity of the rotor winding, the copper strips are coated with insulation material. This coating acts as a protective layer, safeguarding the copper from environmental factors and potential damage during operation.
Winding Process:
The insulated copper strips are meticulously wound onto the rotor, following a predefined pattern. This winding process is crucial, as it determines the efficiency and performance of the electric motor or generator.
Testing and Quality Assurance:
Rigorous testing procedures are employed to ensure the integrity of the rotor winding
copper strips. This includes checks for conductivity, insulation resistance, and overall structural integrity. Only strips that meet stringent quality standards proceed to the final assembly.
The Role of Rotor Winding Copper Strips in Electrical Systems:
Conductivity:
Copper's exceptional conductivity ensures efficient transmission of electrical currents, minimizing energy loss and enhancing the overall performance of electric motors and generators.
Durability:
The durability of copper strips contributes to the longevity of the rotor winding. This is particularly crucial in applications where the motor or generator is subjected to continuous operation and varying loads.
Heat Dissipation:
Copper's high thermal conductivity aids in dissipating heat generated during operation, preventing overheating and maintaining optimal working conditions for the electrical system.
Conclusion:
Rotor winding copper strips may seem like humble components, but their role in the world of electrical engineering is nothing short of paramount. As we continue to advance in technology, the demand for efficient and reliable electrical systems grows, underscoring the importance of quality materials like rotor winding copper strips. Understanding and appreciating the intricacies of these components brings us closer to the marvels of electrical engineering, where seemingly simple elements power the complex machinery that drives our modern world.